Ученые института высокотемпературной электрохимии УрО РАН уделяют большое внимание работе в рамках наиважнейших научных направлений, определенных руководством страны. Так, в 2014 году ИВТЭ УрО РАН принял участие в конкурсе федеральных целевых программ Министерства Образования и Науки РФ «Исследования и разработки по приоритетным направлениям развития научно-технологического комплекса России на 2014 – 2020 годы». Итоги конкурса принесли ИВТЭ большой успех, ведь институтом было выиграно сразу три заявки на проведение прикладных научных исследований. Тематика работ, представленных на конкурс ФЦП, имеет огромное значение для развития экономики и промышленности РФ, в реализации которых заинтересованы такие крупные предприятия, как «ОК РУСАЛ», «ГНЦ НИИАР», «Газпром», НПЦ МГД, Красноярский алюминиевый завод, ООО НПФ «Сосны», ОАО «СвердНИИхиммаш». Именно эти предприятия выступают в качестве индустриальных партнеров ИВТЭ в трех выигравших проектах:
- Разработка энергосберегающего способа получения алюминия, содержащего бор или скандий с использованием расплавленных солей
- Разработка нового токоподводящего анодного узла электролизёра Содерберга ОАО «РУСАЛ Красноярск»
- Разработка научно-технических решений пироэлектрохимической переработки отработавшегоядерного топлива (ОЯТ) в замкнутом топливном цикле (ЗЯТЦ) ядерных энергетических установок с использованием расплавленных солей
О новых технологиях получения сплавов алюминия с использованием расплавленных солей
Быстрые темпы развития передовых технологий (Hi-Tech), роботосроения, автомобилестроения и аэрокосмической отрасли, а также новые требования к эксплуатационным характеристикам сплавов представляют собой большой научный потенциал в сфере разработок лигатур, сплавов и композиционных материалов. Так, Сплавы алюминия со скандием обладают сочетанием уникальных свойств (повышенной прочностью, пластичностью, коррозионной стойкостью), однако использование их очень ограниченно из-за высокой стоимости лигатуры Al-Sc. В свою очередь, сплавы алюминия с бором обладают большей электропроводностью, высокими прочностными характеристиками, и могут использоваться в качестве относительно недорогого армирующего материала; лигатура Al-B применяется для очистки алюминия от переходных элементов, повышая его чистоту и улучшая эксплуатационные характеристики. Производство лигатур Al-B осуществляет несколько предприятий в мире и сведения о технологии ограничены. В России лигатуры Al-B не производят. Использование расплавленных солей является перспективным направлением для разработки новых технологий задания бора или скандия в алюминий. Снижение энергопотребления и уменьшение материальных затрат может быть достигнуто за счёт выбора состава расплавленной соли с улучшенными эксплуатационными свойствами (высокой электропроводностью, небольшой плотностью, низкой температурой плавления и т.д.), что позволит снизить температуру процесса, уменьшить перенапряжение электродных реакций, повысить извлечение бора или скандия из их соединений, а также организовать одностадийный непрерывный процесс.
Новые технологии получения сплавов алюминия разрабатываются в лаборатории электродных процессов ИВТЭ УрО РАН (Екатеринбург) под руководством директора института, доктора химических наук, профессора Зайкова Ю.П. Проект «Разработка энергоэффективного способа получения алюминия, содержащего бор или скандий с использованием расплавленных солей» (№ 14.607.21.0042 от 21 августа 2014 г.) был поддержан Министерством науки и образования РФ в августе 2014 года.
Исследования фазовых равновесий системы «калий-натриевый криолит – оксид скандия», совместной растворимости оксидов скандия и алюминия в криолитовых расплавах различного состава позволили подобрать расплавленные среды, в которых возможно проводить процесс получения сплавов Al–Sc при таких низких температурах, как 750 °С. Разработанный сотрудниками ИВТЭ УрО РАН новый процесс, учитывающий как химическое, так и электрохимическое восстановление скандия и алюминия из их оксидов, будет испытан на крупномасштабной лабораторной экспериментальной установке уже в 2015 году.
Взяв за основу алюмотермический способ получения Al-B лигатур, ученые ИВТЭ УрО РАН значительно усовершенствовали его, разработав новые составы расплавленных солей – флюсов, обладающих улучшенной протекторной функцией и эффективной рафинирующей способностью, пониженной плотностью, а также низкой температурой плавления. С использованием флюсов нового состава в лабораторных условиях была получена лигатура Al-B с содержанием бора 4 % и с равномерным его распределением; разработаны лабораторный технологический регламент и эскизно-конструкторская документация на экспериментальную установку для получения сплава Al-B в составе печи, магнитогидродинамического вращателя, конвейера и укладчика продукции.
Совместно с индустриальными партнерами проекта Научно-производственным Центром Магнитной Гидродинамики (НПЦ МГД, Красноярск) и Красноярским алюминиевым заводом (РУСАЛ) и на их производственных площадках изготавливаются и монтируются экспериментальные установки для получения сплавов Al–Sc и Al-B по новым технологиям.
О технологии нанесения новых защитных покрытий на анодные токоподводы электролизеров Содерберга
Технологии, связанные с производством алюминия, безусловно, вызывают огромный научный интерес, особенно для металлургической промышленности. Так, метод электролитического получения алюминия в настоящее время является одним из наиболее энергоёмких, а Объединённая Компания РУСАЛ – одним из основных потребителей электроэнергии в России с объёмом производства свыше 4 млн. тонн металла в год и удельным потреблением электроэнергии 14 – 16 МВт*ч на тонну алюминия.
В соответствии с одним из приоритетных направлений развития науки и технологии России ОК РУСАЛ проводит мероприятия и осуществляет разработку новых технических решений, направленных на снижение расхода электроэнергии при производстве первичного алюминия без глубокой модернизации находящихся в эксплуатации электролизеров и существенных капитальных затрат.
Большой потенциал для снижения энергетических потерь заложен в модернизации токоподводов – конструкций, осуществляющих подведение тока к электролизной ванне. Наименьшим сроком службы до 48 месяцев, а в последнее время – до 24 месяцев, обладают анодные токоподводы, которые эксплуатируются в составе анодного узла электролизёра при температуре до 900 °С.
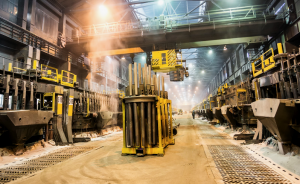
Электролизёры Содерберга с верхним токоподводом на площадке ОАО «РУСАЛ Красноярск». В центре – кассета с анодными токоподводами перед установкой в ванну
В ходе выполнения работ по проекту «Разработка нового токоподводящего анодного узла электролизёра Содерберга ОАО «РУСАЛ Красноярск» (№14.607.21.0035 от 5 июня 2014 г.) было отмечено, что сокращение ресурса анодных токоподводов связано с ростом концентрации серы в углеродсодержащем сырье, применяемом при производстве анодов. Взаимодействие с серой и образование слоя сульфида железа на поверхности стальных токоподводов приводит к снижению их электропроводности и увеличению удельного расхода электроэнергии. Оксидно-сульфидные продукты коррозии, попадая в ванну, дополнительно загрязняют алюминий.
Основными задачами, поставленными перед сотрудниками ИВТЭ УрО РАН в ходе реализации проекта, являются обеспечение высокой электропроводности анодных токоподводов и повышение их ресурса без снижения сортности производимого металла.
В качестве возможного решения было предложено защитное коррозионностойкое покрытие на основе алюминия и методы его нанесения с применением расплавленных солей. Расплавы на основе фтористого алюминия с добавками фторидов щелочных металлов, используемые в технологии электролитического получения алюминия, обладают относительно высокой растворимостью оксидов металлов. Это свойство расплавов применили в разрабатываемой технологии нанесения покрытия. Эффективное растворение оксидных плёнок с поверхности стальных токоподводов позволило повысить качество покрытия без применения защитной атмосферы и сократить количество технологических операций.
В прошлом 2014 году был успешно завершен первый этап работ: проведены лабораторные исследования коррозионной стойкости стальных токоподводов с защитным покрытием в условиях, соответствующих условиям их эксплуатации в электролизной ванне. Было показано, что применение качественного алюминидного покрытия обеспечивает многократное повышение жаростойкости стального токоподвода на воздухе и защиту от серной коррозии. В настоящее время ведутся подготовительные работы для проведения испытаний уже в промышленных условиях – на электролизёрах ОАО «РУСАЛ Красноярск». В ходе выполнения проекта также будет спроектирована и изготовлена установка для дистанционного определения коррозионного износа токоподводов на основе 3D-сканирования их геометрических размеров. Она позволит более точно установить эффект от применения экспериментальных токоподводов с защитным покрытием.
О замкнутом топливном цикле ядерных энергетических установок
Еще одно направление, интерес к которому заметно возрос в последние годы – исследование солевых расплавов как перспективных рабочих тел ядерных энергетических установок, сред для переработки природного и техногенного сырья, содержащих редкие и радиоактивные металлы, радионуклиды и другие продукты ядерных реакций. Стратегия развития современной атомной энергетики базируется на принципах, обеспечивающих естественную безопасность ядерных реакторов, исключающую аварии с выбросами радиоактивных продуктов в природную среду; режим нераспространения; замыкание топливного цикла атомных электростанций; воспроизводство ядерного горючего. Солевые, особенно фторидные и хлоридные расплавы, как никакие другие жидкие среды (вода и органические вещества), благодаря своим уникальным свойствам (термической и радиационной стойкости, высоким электро- и теплопроводности и др.) могут успешно использоваться в атомной энергетике как топливные композиции жидкосолевых ядерных реакторов «естественной безопасности», бланкетов, теплоносителей и регенеративных сред при переработке отработавшего ядерного топлива (ОЯТ). Они обеспечивают выполнение необходимых условий для разработки атомных электростанций с замкнутым ядерным циклом (ЗЯТЦ), возвращающим в топливный контур обогащенное ядерное горючее, а также существенно уменьшающим объемы «долгоживущих» радиоактивных продуктов деления, предназначенных для «захоронения», исключая, тем самым, вредные факторы воздействия на человека и окружающую среду при эксплуатации атомных энергетических установок.
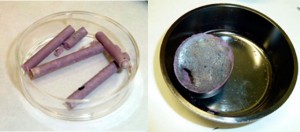
Электролиты с разным содержанием соединений урана, подготовленные к пироэлектрохимической переработке
В конце прошлого года проект ИВТЭ УрО РАН на тему: «Разработка научно-технических решений пироэлектрохимической переработки отработавшего ядерного топлива (ОЯТ) в замкнутом топливном цикле (ЗЯТЦ) ядерных энергетических установок с использованием расплавленных солей» (№ 14.607.21.0084 от 31.10.2014 г.), который выполняется вместе с Научно-исследовательским институтом атомных реакторов (АО «ГНЦ НИИАР») и индустриальными партнерами: Научно-производственной фирмой “Сосны” (ООО НПФ “Сосны”) и Свердловским научно-исследовательским институтом химического машиностроения (ОАО «СвердНИИхиммаш») был поддержан Министерством образования и науки Российской Федерации. Эти исследования особенно актуальны в связи с разработкой и вводом в эксплуатацию реакторов нового поколения типа «БРЕСТ» с нитридным уран-плутониевым топливом, в один из вариантов комплексной переработки которого включен пироэлектрохимический передел. К настоящему времени проведен анализ научно-технической и патентной литературы, определены направления комплексных исследований физико-химических свойств реакционных сред, окислительно-восстановительных реакций, коррозии конструкционных металлических сплавов, выбраны способы переработки ОЯТ и моделирования электрохимических процессов в галогенидных расплавах, выполнен комплекс экспериментальных работ.
Творческим коллективом, который включает более десятка высококвалифицированных специалистов и молодых сотрудников лаборатории расплавленных солей ИВТЭ УрО РАН получен ряд новых результатов,
необходимых для успешного решения поставленных в проекте задач:
– предложены и испытаны способы синтеза чистых хлоридных электролитов-имитаторов, свободных от примесей кислородсодержащих соединений и воды, которые являются «ядами» при пирохимической переработке ОЯТ;
– изучена кинетика взаимодействия нитрида с рабочим расплавленным электролитом;
– измерены необходимые для технологических расчетов температура ликвидуса, теплоемкость и теплопроводность расплавов, содержащих соединения урана и редкоземельных металлов;
– разработана модель процессов пироэлектрохимической переработки отработавшего топлива ядерных энергетических установок в галогенидных расплавах и проведены расчеты тепловых, концентрационных и электрических полей в опытном электролизере, предназначенном для переработки ОЯТ в хлоридном расплаве.
Нашими индустриальными партнерами выполнены работы по подготовке исходных данных и разработке технического задания и конструкторской документации на изготовление
экспериментального образца установки для диагностирования электрохимических процессов в галогенидных расплавах.
Одним из самых важных и полезных следствий выполнения работ по проекту является установление прямых деловых контактов с организациями и предприятиями Госкорпорации «Росатом», позволивших понять сложность проблем по организации замкнутого топливного цикла атомных электростанций и уточнить задачи по пироэлектрохимической технологии переработки ОЯТ.
Все работы проводятся при финансовой поддержке Министерства Образования и Науки РФ по соглашениям о предоставлении субсидии №14.607.21.0035 от 5 июня 2014 г. (RFMEFI60714X0035), № 14.607.21.0042 от 21 августа 2014 г. (RFMEFI60714X0042), № 14.607.21.0084 от 31 октября 2014 г. (RFMEFI60714X0084).
СМИ о нас: http://uran.ru/node/4179